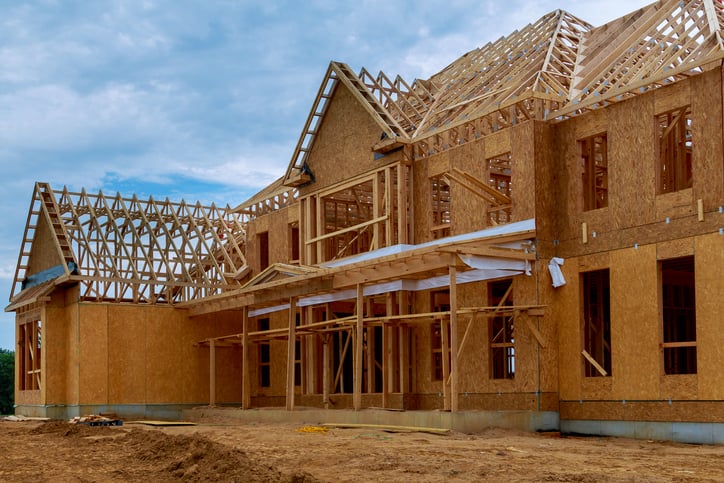
For those looking to go the prefab route to build a custom home in Western New York, there are two routes: modular home building or panelized construction.
Our specialty is panelized construction – a building method we’ve fine-tuned during our decades of business. As thousands of happy Barden homeowners have found, panelized construction was an efficient process to get them a 100% customizable home without cutting corners on one of the biggest investments they’ve ever made.
But what about the other option?
To hear some (our competition) tell it, modular building is the better option. They’ll say the modular home timeline for construction is faster and that the modular home cost is lower.
Is this all true?
Several years ago, we spoke with a former salesperson for a WNY modular home company to get some insights
The result?
Even with our affinity for panelized construction, we found that modular homes aren’t always faster or cheaper to build for those looking for a custom home. Our conclusion(s) about the modular home timeline still holds today.
Why the Modular Home Timeline in WNY (or Anywhere) Isn’t Cheaper or Faster to Build
In reviewing the conversation we had with our competition, we found there are 4 common reasons why WNY modular home timelines are the fastest or cheapest option for new home construction:
- The production deposit was financed
- The customer wanted a custom floor plan
- Elements of a custom floor plan could not be factory-built
- Non-standard materials were specified
Let’s explore how each of these reasons impact the modular home build timeline.
-
The Production Deposit Was Financed
When a modular manufacturer begins building custom homes in their factory, they require a production deposit between 10%-50% of the total cost of their manufactured product.
If you have that much money to put down on the new home, things get rolling right away with no delays.
However, if the production deposit is coming out of a construction loan, you might have to wait up to 2 months for the deposit to be released, which adds at least 2 more months to the build time!
What’s more, you may be in line for more delays. Most construction loans have a funding release schedule that’s dependent on the project reaching certain milestones. Depending on the structure of your loan and exactly how your modular home builder completes work, you might end up pushing move in day back more than you originally anticipated.
What do you need to know about financing your panelized custom home construction project? Check out our finance guide:
2. The Customer Wanted a Custom Floor Plan
There are “custom” modular home companies all over Western New York and the Northeast.
And although these companies can customize a floor plan, it takes a lot of extra time. This means you’ll have to wait longer to move into your custom home – another ding to the modular home construction timeline and modular home cost.
Substantially customizing modular floor plans add extra time and engineering costs because essentially you’re starting from scratch. Modular home floor plans are designed to be structurally sound and quickly produced. Veering away from the provided layout means someone has to at least evaluate the plan for soundness and safety, which might result in some substantial alterations to the home’s structural elements.
What’s more, there’s also the matter of getting the home to your build site. In some cases, a modular home with a custom floor plan needs to be engineered from scratch to be transported (sometimes hundreds of miles). A crane must be capable of lifting it without breaking any of the valuable pre-installed items or cracking any drywall.
3. Elements of a Custom Floor Plan Cannot Be Factory-Built
This one is simple. Because of how a modular home is built in a factory and transported to the build site, there are limitations on the custom home features that are possible for it. Another way: there are some custom home elements that simply can’t be built in a factory with a modular home, such as:
- Attached garages
- Vaulted ceilings
- Covered porches
- Open-concept floor plans
Even 9’ or 10’ ceiling heights are tough to manufacture in a factory.
For modular home floor plans including these elements, those building the home had to add these features on-site during construction. This added time and labor costs to completing the home.
Add in the fact that these jobs are small, and the contractors performing the work won’t be very inclined to make the job a high priority or provide competitive pricing.
Put simply: More customization options to complete on-site means the chance for delays increases exponentially.
4. Non-Standard Materials Are Specified
For first-time future homeowners, it might seem reasonable to think you’d have a say in the finishing elements of your new home.
Maybe you’re expecting to pay your nearest kitchen design center a visit and pick out custom kitchen cabinets and countertops? Or perhaps there are some windows you liked at a home show that would look perfect in your new home?
As we found talking to the competition, while many WNY modular home companies do allow for custom choices like these, they become a source for constant delays and problems. That makes sense.
If a modular home engineer is used to designing every window opening for a certain window, every single window opening will need to be redesigned to accommodate an unfamiliar manufacturer's window. The same goes for every single installer on the production line.
Unfamiliar products require a learning curve, which means there’s a higher chance the products are installed incorrectly and a definite chance they’ll take longer to install. And that’s even if the company allows their customer to make choices like this.
The TLDR: non-standard materials can hinder modular home construction speed.
Panelized Homes: The Faster Option?
As much as we’d like to give a resounding “yes!”, this one can be tricky to answer.
Why?
Because so much of a panelized home’s construction timeline depends on the future homeowner.
Unlike modular building, panelized construction allows for 100% customization. That means everything from the layout to the countertops can be adjusted to the owner’s wants and needs. As we’ll always point out, we don’t think any of our Barden Indpendent Dealers have ever built the same home twice because homeowners always make at least a tweak to two to a floor plan.
It’s worth noting, if you come to the table prepared – meaning, you have a good idea of what you want from your custom home, you have the build site already, and your finances are in order – the panelized construction process can be incredibly efficient when compared to modular construction and traditional stick building.
The same overarching principle applies to a panelized custom home’s cost. We’d love to give a hard figure for how much a Barden home costs. But with all the floor plans available and options for them, coupled with how fast the future homeowner is looking to (or is able to) move, it’s nearly impossible.
Again, the speed and cost in which a panelized custom home project is realized and its cost largely depends on the future homeowner.
WNY Modular Home Timeline: Our Verdict
Are modular homes ever a more efficient and cost-effective choice?
In a certain set of circumstances. They can be a good option for those who have their finances in line before construction and are OK with the standard options included in a floor plan. In other words, they’re ready to buy now and are good with a floor model. In our book, that’s not custom home building, and it’s not that much different than buying a home that’s on the market.
But your future custom home is where you’re going to live for some time. Shouldn’t it be designed to meet your needs, stay within your budget, and be built without delay?
With panelized construction, it’s possible to get all of the above.
Learn More About the Panelized Construction Timeline
Check out our Custom Home Building Checklist!