In most cases, those who become one of our independent dealers already have an established home building company.
Such is the case with Severyn Development. A Lancaster, N.Y.-based construction firm, Severyn had long been doing business in Western New York before becoming one of our Barden Independent Dealers.
For those considering following suit with their home building business, you’re probably wondering what becoming a Barden Independent Dealer will mean for your business.
In Severyn’s experience, it meant they were able to our our suite of products and services to their offerings. They were also able to take advantage of the support we offer our dealerships, such as help with marketing or access to our Drafting and Design Department. They didn’t have to reinvent their business or operate within a set of strict parameters.
The same will apply to your dealership.
In 2019 we sat down with Will Severyn for a brief chat about his experience using our panel home construction process and our products after joining us as a Barden Independent Dealer. His impressions and experiences still hold true today.
Q. What Brought You to Barden?
A. The very first thing that brought us in was building on infill property. So here in Buffalo, what I believe is going to be a very popular way of building in the future, is we’re taking old city and village properties in dense areas where people want to live, and there’s no room to stage. When we started building stick frames in the suburbs and we had 75’ x 150’ lots, we could get a forklift around and have materials delivered, no problem. Now though, working in the city, what we like is that we can set the deck on the foundation the first day, the next day the walls show up, the next floor the next day, trusses the next. By redesigning and reengineering how our buildings are installed, we don’t have any waste, we aren’t moving things twice, and we don’t have any dumpsters during framing.
Q. After Working With Barden for a Few Months Now, How Has Our System Changed How You Plan Projects?
A. First, it’s shortened our custom home building timelines. On one of our hardest projects (1016 Lafayette) that you guys came in and framed for us, it took us two-and-a-half weeks to frame the garage, and Barden had the house up in about 6 days. Now that saves a lot of time and a lot of frustration for our clients. Again we’re building on tight sites, so it’s stressful. The minute that structure is up, the whole project gets a lot easier.Our floor plans are changing to include more truss work, we’re looking to utilize floor truss systems for longer spans - we’re getting a lot of requests for more open living spaces.
When we go to build duplexes, income units, things of that nature, we have the same price for the lumber package every time. When I go to build an investment property, I want to know what it’s going to cost based on what the last one was, and you guys are the ones able to do that. I used to work with other lumber suppliers, and they would do the take-off to the best of their ability from the plan, but our framers still had to call in for more lumber. What happened was that we never had two projects that looked the same. With Barden we can engineer it, pre-fab it, and know that it’s going to be the same price and nothing is going to be wasted. I even had contractors calling in extra lumber that wasn’t necessary. So now there’s no add-ons; the lumber is all there, pre-cut and labeled, and I know I’m not wasting any money.
Q. Has Switching to Barden Changed Your Process?
A. It doesn’t change the process, I don’t think anyone should look at this as an overhaul of their construction process, but it does make it quicker.
Q. How has the feedback from your contractors and customers been since switching to Barden?
A. Our project managers love the Barden system. The windows come out better, the framing comes out quicker, and there are fewer change orders. Basically what we’re forced to do, in a good way, is confirm our floor plans with our clients ahead of time. It might take a little longer to get started, but by presenting the Barden system they understand that once it’s engineered it’s going together one way. That really allows us to move forward with the project ordering the trim, the siding, the doors, and the windows. We know that the floor plan isn’t going to change, where in the past I’ve had stick frame projects where because making changes are still an option, we have changes to window sizes and room dimensions that make planning for the next phases much more difficult.Q. We’ve talked a lot about infill lots, but you have done some patio homes and single-family homes in the suburbs with us as well. What has your overall impression been based on all of the jobs you’ve done with us so far?
A. With the cost of construction, the way it increases, and the way that it changes - seasonality, market, contractor availability - all those factors are variables that we have to estimate when we do our construction. Lumber and framing should not have to be one of those variables, but that’s how it is when you enter a stick frame project. You have an estimate, it’s your best guess, but it changes dramatically throughout the project. So what we like, whether it’s a custom home or an income property or a standard single-family house, we like that when we start the project we know the lumber cost and it does not change.Q. Outside of the obvious material and labor costs, what other savings have you seen?
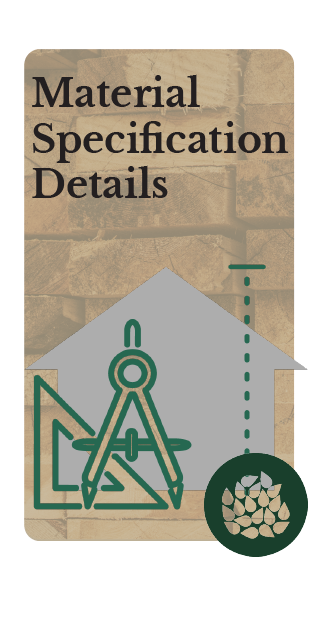
Time is huge too. When our best crew did one of our patio homes, the crew has 9 guys, it took them a week to frame. Barden showed up with 3 guys and it took them 3 days. Framing to us, especially where we build, needs to be a fast process. We can get a roof on a house 3 days after we lay the decking on the first floor.
We don’t have access to framers right now because they’re tied up on their last project for too long. We have to have some of that labor done ahead of time to keep control over the project. With Barden, you guys are going to have a house a week framed for us with a single crew.
Take the Next Step
Interested in learning more about our panel home construction process and Barden Independent Dealer program? Download our e-book: "Becoming a Barden Independent Dealer: A Blueprint for Success":